The game-changing plan to put rare classics back on the road
Specialists believe that new advances in 3D printing could be a ‘game-changer’ for the classic car sector
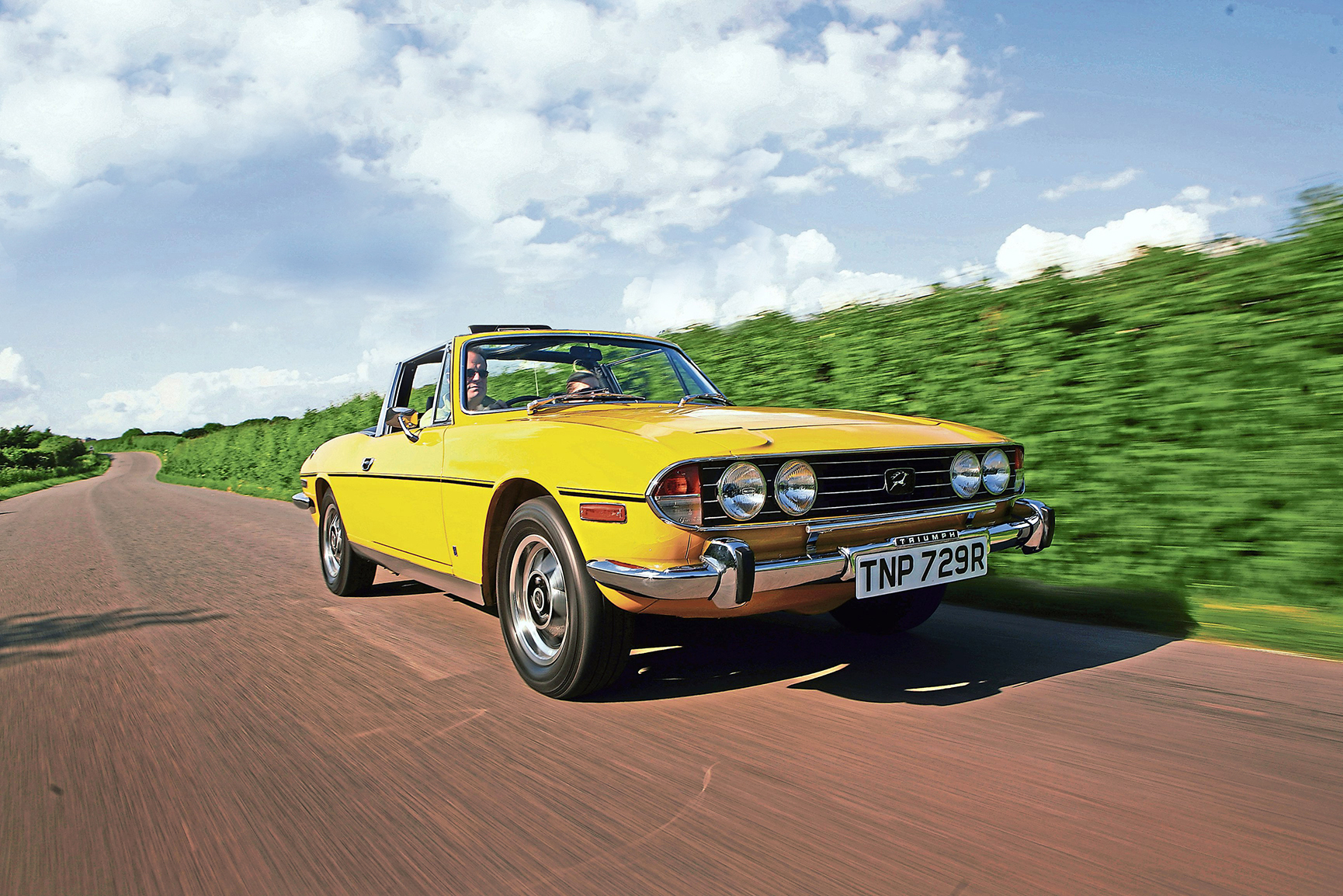
A new solution targeted at bespoke low-volume work including ‘reverse engineering’ using 3D printing in plastic and metal could help guarantee the continued parts supply for many classics. That’s the word from the Federation of British Historic Vehicle Cubs (FBHVC)’s Spares Working Group for clubs that supply spares to share information and best practice.
The Federation has announced a partnership with Igus Motion Plastic – a German injection moulding specialist that has its UK base in Northampton – that will enable clubs to order parts made to order in very small production runs, enabling spares to be made in quantities that would otherwise have been prohibitively expensive.
Igus product manager Alan Hicks was also invited to speak at the Federation’s recent Club Expo about the Production of non-available parts. Igus produces a vast array of parts that are shipped globally but also offers multi-material 3D print parts ranging from prototypes and those produced in small quantities to high-volume production.
Speaking at Club Expo, Alan said: ‘I am aware that there are a lot of obsolete parts that you cannot change on classics. We have our own online tool that is free to use to generate a drawing, so you don’t have to find somebody to draw a part for you. If it’s too complex for you to draw on our website you can contact us, send us the part and we can 3D scan it and generate a drawing for you and then offer a price for producing it.’
‘This is a major step forward for clubs looking to produce small runs of parts that are not otherwise available’
– The Federation of British Historic Vehicle Cubs
The FBHVC also published a Guide to Parts and Services in an ‘Essential Guides’ series for clubs and last year’s Club Expo included a presentation from the Stag Owners’ Club Tooling Fund, explaining how it assesses demand and commissioning parts that are no longer available, such as door handle bowls.
The FBHVC’s communications director, Wayne Scott, said: ‘Clubs need to address parts quality and supply issues more and more, as the profit in small runs of components is not high enough for most commercial suppliers to justify production. Clubs have the advantage of only needing to cover costs rather than make a profit and making parts available to members only gives clubs compelling reasons to join and renew.
‘Igus provides an online design, prototyping and manufacturing service with all of the help, advice, and experience that clubs need to make small runs for parts. Its minimum order is one!
‘This is a major step forward for clubs looking to produce small runs of parts that are not otherwise available. It opens up huge opportunities and the FBHVC has been proud to present this partnership for clubs’ benefit. Furthermore the FBHVC partnership with Peter James Insurance offers product liability cover to ensure that clubs are adequately protected for the parts that they sell.’
‘IT COULD BE A GAME-CHANGER’
I think that 3D design and printing is a great addition to what may become one of the classic car industry’s biggest challenges. Within my own business we have used companies to reproduce obsolete clips and fascia parts. It is a capability that we are hoping to bring in-house and it is certainly an opportunity for a new generation of entrants to our industry to develop specialist skill sets outside of the ‘conventional’.
I think it could be a game-changer as 3D scanning and printing technology becomes more affordable and the capability to work with ever more diverse materials increases. I would add one caveat, because of the time involved the parts won’t ever be as cheap as mass-produced batches; that said if the option is there to pay the money and have that part or have no part at all I think people would be prepared to pay. It’s a very positive contribution.
DOMINIC TAYLOR-LANE ASSOCIATION OF HERITAGE ENGINEERS